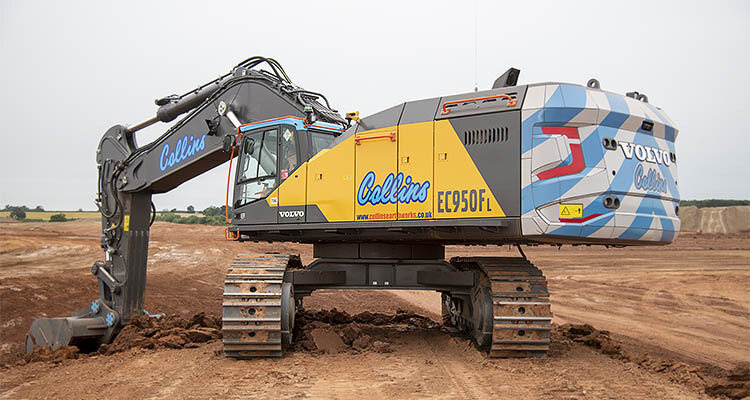
Collins Earthworks sets self-sufficient standards, raising the bar in construction
With a proud history that spans over 20 years, Collins Earthworks Ltd (Collins) is a pioneering leader in the field of earthworks and civil engineering. Based in Ripley, Derbyshire, the company has successfully executed numerous high-level infrastructure and enabling projects throughout the UK, including the East Midlands Gateway, Northampton Gateway, HS2, and Grantham Bypass.
Renowned for its expertise across multiple facets, Collins operates through six affiliated companies, each specialising in a distinct area. These subsidiaries include divisions dedicated to Earthworks, Demolition, Stabilisation, Transport, Training and Plant Sales.
This diversified approach allows Collins to offer turnkey solutions tailored to the specific requirements of each client. Company Pre Construction Manager, Adam Green, sheds some light on the company’s early days. “The business was started many years ago by David Collins, firstly as a sole trader, then registering Collins Contractors Plant Hire Ltd in early 2000. Since its early establishment, the business quickly evolved and began expanding to become the successful enterprise it is today. In 2006, the trading name was changed to Collins Earthworks Ltd, which is the main parent company focusing on bulk earthwork operations. Following the continued expansion of its earthworks division, EnviroTrac Ltd was founded in 2008. EnviroTrac is our ground stabilising division focusing on using lime and cementitious binders to treat and modify heavily saturated soils that produce a high bearing capacity. Succeeding EnviroTrac was Collins Training developed in 2013 to offer in-house training to both internal staff and external clients. As a result, over 90 per cent of our operatives are provided with in-house qualifications and training, all the while continuing to serve external clients. Three years later, we formed Collins Demolition Ltd to handle all site preparation and clearance works to facilitate our earthworks operations. This subsidiary has recently expanded its asbestos division listed as a licensed asbestos contractor as well as recently joining the NFDC in 2022. On the back of that, Collins Transport Ltd was incorporated in 2018, which oversees and manages more than 7000 yearly movements of heavy plant and equipment nationwide. Our fleet consists of road sweepers, eight-wheelers, artic tippers and heavy-duty low loaders specifically designed to transport plant and equipment to designated projects. Lastly, the final addition to the business was Collins Plant Sales Ltd, which was established in 2019. This subsidiary obtained an agreement with Volvo to be their main dealer covering Derbyshire, Nottinghamshire, and Lincolnshire. Collins Plant Sales supplies the full Volvo range of compact excavators from 1.5-to-nine-tonne, wheeled loaders, as well as tandem asphalt compactors. The creation of these companies was developed to offer full-package solutions to our clients without the need for extensive external support and resources. This approach has been a fundamental part of Collins’ development and growth,” he enlightens.
Diverse challenges
Self-sufficiency is one of the leading qualities of the company today, making it a versatile and reliable all-inclusive solution provider for customers. “I believe the large-scale enabling projects we work on best demonstrate our self-reliance,” Adam begins. “We are often approached to carry out schemes listed as ‘Gateways’ due to successful delivery of previous projects and it is what the company is built for,” Adam continues. “Typically, we are assigned ‘Gateways’ spanning millions of square meters, in which we carry out everything from the initial site clearance works to the final stages of earthworks involving the constriction of numerous engineered plateaus and infrastructure works for future development. One live project that best represents this is Northampton Gateway. This site is located just off Junction 15 of the M1 and spans over two million square metres. On this particular scheme, we are contracted to cut and fill over four million cubic metres of material across a series of plateaus, rail freight terminals, and infrastructure works. To give you an idea of outputs for this specific contract, we’ve moved in excess of 120,000 cubic metres of material per week during peak times across the project!” Adam explains. “After completing the enabling works, our focus shifts towards the necessary earthworks and aggregate importation that will be needed to complete vertical build stages of individual distribution sheds or warehouses. This approach forms the basis of our involvement in most ventures we undertake the length and breadth of the UK.
“However, we don’t stop at ‘Gateways’ and distribution units, as we also expanded our scope to include large-scale civils, highways and infrastructure projects. This includes projects such as Grantham Bypass and Melton Mowbray Distributor Road. We are also engaged in significant sections of HS2 and recently secured a highway scheme in Milton Keynes. Diversifying our portfolio and venturing into various projects adds a pleasant variety to our workload,” he says.
Nathan Warner, Surveyor and Head of Marketing, affirms that the variety of projects is one of the many reasons why he enjoys working at Collins. “While industrial sheds and related projects remain our core expertise, the opportunity to work on diverse projects keeps things interesting as we get to regularly encounter different challenges. It’s especially nice if you genuinely enjoy construction and want to be involved in new, varied projects each day. Collins is a great company to work for to get the thrill of constantly embracing fresh endeavours,” he confides. Nathan emphasises that the company culture plays a significant role in making Collins an appealing company to work for. “There is a distinct sense of a professional, family-like atmosphere within Collins. Although we have experienced tremendous growth over the last few years, the managers and key leadership remain actively involved in all projects and present throughout every stage. This level of hands-on engagement is one of the things I really appreciate about our culture. Furthermore, another aspect I thoroughly enjoy about working here is the diversity of people we collaborate with, both within the company and among our clients,” he explains. “The routes for progression are endless. The majority of management has risen through the company ranks along with numerous individuals still present from the early establishment.”
Teamwork, technology and client satisfaction
Collins’ emphasis on fostering a positive work environment and being self-sufficient proved to be especially advantageous during the pandemic and other industry challenges. “The construction industry as a whole has faced numerous challenges over recent years including Covid-19, changes to government legislation and rising material/fuel costs following Eastern European conflicts.” However, despite challenges the company remains poised to thrive through its adaptable strategies, ensuring a promising future. Adam adds: “We are pushing both sustainable and low-carbon solutions to our projects including investments in hybrid machines and the use of all fully electric artic tippers which are set to land in Q4 2023. We have also recently purchased Ball Eye Quarry located in Derbyshire which is set to be operational towards the end of 2023. Having our own quarry opens further opportunities for the business allowing us to supply our own certified aggregates directly to our projects throughout the UK.”
Looking back over the history and evolution of Collins, it is evident that this is a contemporary and adaptable business, melding the traditional values of quality, service, and experience with modern and forward-thinking approaches. Not one to shy away from complex and challenging projects, the company continues to deliver success and maintain its reputation by combining teamwork, technology, and an unyielding focus on client satisfaction.