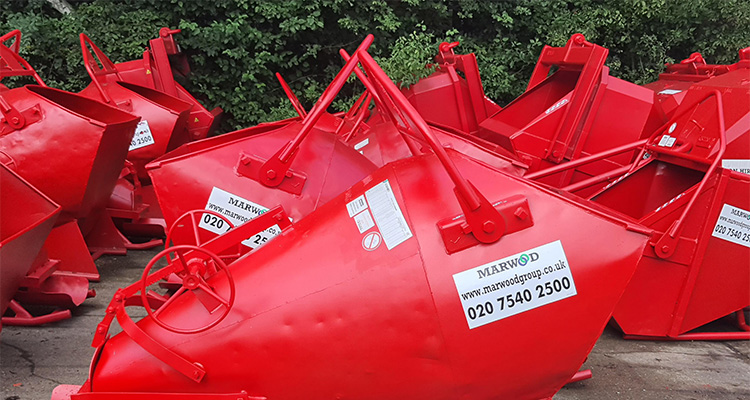
Dive into the intriguing rise of Marwood Group Ltd in the non-mechanical rental industry
With over 45 years of experience in non-mechanical products (such as barriers and skips), Marwood Group Ltd (Marwood) boasts a wealth of knowledge and technical expertise to effectively serve its customers. Amidst an ever-evolving landscape and new norms, the company is actively involved in one of Europe’s largest construction projects, a testament to its reliability and adaptability. To guarantee the quality of its products, Marwood operates from its very own bespoke steel and plastics manufacturing facilities. Through its steel manufacturing centre, it has the capability to design, construct, and provide services for both its own products and those requested by customers. Meanwhile, its plastics factory enables the production of high-quality plastic barriers and traffic demarcation products. Jeff Gold, Sales Director, provides a comprehensive introduction to the business.
Strategic acquisitions
“In its infancy, Marwood was a light demolition and building works contractor, with a head office and light engineering facility in Silvertown, East London. However, in the early 1980s, we started renting out our fleet of compressors, tools, steel plates, acrows and crane skips. Soon enough, this business model proved more profitable than any previous building contracts. Recognising this trend, our owner, Charles Martin, made the strategic decision to shift our focus exclusively to product rentals and cease all contracting activities. Given their scarcity in the marketplace, non-mechanical items proved to be particularly popular, prompting us to make niche, non-mechanical hired building products our core offering. This strategic move proved hugely advantageous during the building boom of the late 1980s across the country. To keep up with increased demand, we acquired two additional storage yards, one in Southampton docks and another in Beckton, the latter of which has been our administrative home since. I joined the company in 1989, just before the establishment of a second depot at the Southampton docks site,” he opens.
“Over the course of the next 20 years, we significantly expanded our non-mechanical product range, driving us to purchase 16 sites to ensure comprehensive geographical coverage. In 2008, we acquired Railtec Engineering, a steel fabrication company. As a result of this acquisition, we were able to assume control over the supply chain and guarantee the ongoing quality of the crane and forklift products made for our hire fleet. To accommodate our expanding operations, we relocated to a larger, purpose-built facility in Maplewell, Barnsley. This move empowered us to enhance our steel fabrication capacity and offer improved design and build services to our customers. Subsequently, we purchased a plastic manufacturing company called Europalite in 2014. It is worth noting that we retained its original name while placing it under the Marwood umbrella. Acquiring Europalite has proved highly beneficial in manufacturing our own product for hire and sale.”
Prioritising sustainable products
Powered by these acquisitions and an improved product portfolio, Marwood’s growth has been off the charts. To accommodate its expanding needs, the company purchased a new depot in Dagenham. “In 2018, we realised that our facility in Barking was not large enough to meet the growing demand. It took a few more years until we could find a property that could offer us the appropriate yard space, offices, and workshop facilities to establish it as our flagship site. This project represents a substantial investment of £16 million in the site, along with £1.5 million in upgrades. Upon obtaining ownership in December 2023, we started the refurbishment project in late January 2024. Our plans encompass a full office refit, full engineering works within the warehouse, and yard upgrades. Currently, the engineering fit-out is progressing well, with our shotblast and paint spraying sheds already in place. Moreover, the office renovations have been completed, and we have begun moving some inventory onto the site ahead of our opening in August 2024. Once finalised, our facility will be equipped to service London with our extensive non-mechanical products available for hire and sales. Additionally, we will offer our customers a comprehensive customer-owned product refurbishment service. Overall, our new Dagenham depot marks a significant step forward in being able to deliver more of our high-quality product across the South and support our depot operations nationwide,” Jeff enlightens.
To top it all off, Marwood has formed a partnership with Richards CCTV, which has provided invaluable support in implementing the security measures at its new Dagenham depot. “We have turned to Richards CCTV to assist us in setting up a security video system covering our premises for both security and employee safety reasons,” begins Jeff. “Given that our new Dagenham depot is our largest facility, replacing the old security system was a major task, which our partner has successfully completed. Ever since our first time working together in 2012, Richards CCTV has been our most trusted security partner nationwide. Our relationship is founded on its expertise in delivering highly capable and reliable video and on-site security systems. Presently, Richards CCTV supplies security to all 18 of Marwood’s locations. Its fully integrated solution allows us to log onto our security system from anywhere in the country, enabling us to view all cameras remotely. Besides, we receive outstanding backup service, with any problems or camera issues swiftly rectified by Richards CCTV’s own skilled engineers,” he goes on.
As our interview reaches its end, Jeff emphasises Marwood’s commitment to sustainability. “Over the last five years, we have placed a greater focus on procuring products that promote sustainability and help reduce our carbon footprint. For instance, within our range of timber excavator and temporary roadway mats, we now prioritise the purchase of sustainably farmed eucalyptus and bamboo mats, thereby preserving rainforests. Within our plastics manufacturing division, we offer a closed loop recycling option, enabling our plastic products to be recycled through our recycling partner. We then acquire the recycled material for future product manufacturing purposes,” he concludes.
Through strategic expansion and a dedication to safety and sustainability, Marwood is set to strengthen its national leadership in product rentals and services.