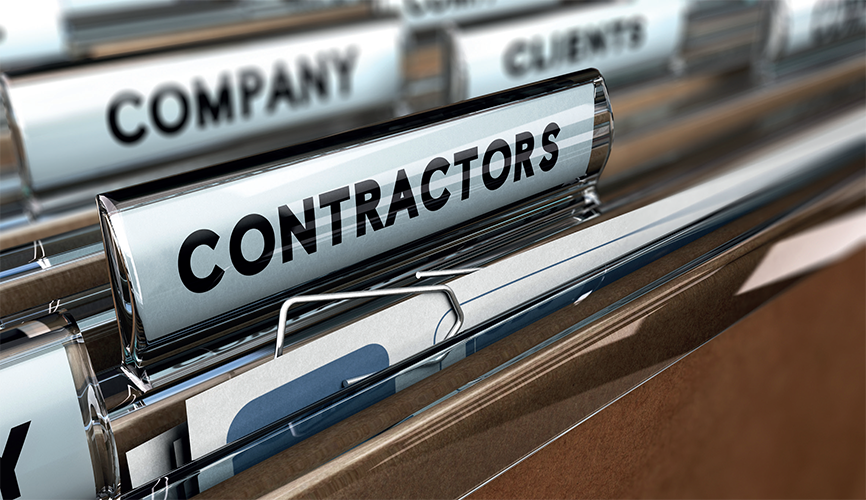
Fail to plan,plan to fail
Modern construction projects are highly complex and as the built environment becomes more ‘intelligent’ the range of skills required on-site at any one time has grown. Acquiring specialist expertise through the use of subcontractors has been part and parcel of the construction industry for decades, and many of the tasks on a construction project are carried out by this resource. Most main contractors are keen to use subcontractors rather than direct labour where possible, as it allows them to minimise direct and indirect overhead costs and benefit from a high degree of workforce flexibility.
Together forever
So, is it a case of if it ain’t broken don’t fix it? Not necessarily. The idea of main contractors and subcontractors working together in perfect harmony through shared values, quality standards and a commitment to keeping a project on schedule is far from the norm. Some industry commentators even argue that the inability of subcontractors to make a meaningful contribution to the construction process under the established procurement system prevents them from improving value on projects and hampers their integration with the rest of the supply chain.
Main contractors and subcontractors tend to pursue self-interest to such an extent that collaborative working is impossible to achieve. The adversarial relationship between the two parties was highlighted in 2019 when Kier announced a plan to charge subcontractors 1.5 per cent of their package turnovers to become closer strategic partners. It claimed that this different approach to supply chains was to encourage greater collaboration, but was met with anger from the wider subcontractor community and subsequently withdrawn. Perhaps not surprising given that over 14,000 suppliers and contractors work with Kier.
Then there’s the payment issue, which has been a persistent problem for many years. A combination of the retentions scheme and a widespread ethos of ‘only pay at the last minute’ have not only created a culture of mistrust and suspicion, but also led to the insolvency of many subcontractors. If a subcontractor experiences late payment, they are entitled to suspend the whole of the works, while a party who validly suspends work because of non-payment is also entitled to reasonable costs and expenses arising from the suspension.
Flip side
As usual, however, there are two sides to every story. While the focus is often on the poor deal that subcontractors have in the construction supply chain, the over-reliance main contractors place on subcontractors can leave them vulnerable and represent a major risk factor. A subcontractor that isn’t meeting its contractual obligations can completely destroy a project schedule and eliminate any profit margin.
This can often be the result of poor administration and financial monitoring, rather than a deliberate intent to default on the work. Subcontractors often have to carry out a significant amount of activity before they start getting paid – a situation that can soon lead to cashflow problems. All too often main contractors fail to spot the signs and react to any red flags, such as a sudden decrease in the subcontractor’s workforce on-site and delayed materials deliveries. Furthermore, a struggling subcontractor can often carry out substandard work and fail to adopt best practice.
They will often try to make up for any shortcomings by further subcontracting out certain elements of the work they have been tasked with, creating an additional layer of complexity. For the main contractor this means that their ability to control a project is further hindered and opens up the potential for more delays. In many respects, it is the practice of subcontractors subcontracting that is the major issue when it comes to the principal goals and objectives of a project being diluted, with sequencing, timescales and quality of work often being derailed.
Long-term thinking
The argument in favour of using subcontractors usually focuses on the cost benefits to the main contractor, especially during quieter periods when they can simply stop using them. However, even during the height of the coronavirus pandemic the construction sector remained relatively buoyant and it is only now experiencing issues around a materials shortage. There’s no doubt that Brexit has also had a significant impact on the number of available construction workers, many of whom have decided to relocate.
This all shines the spotlight on whether main contractors should be focusing on improving their in-house talent pools, driving up knowledge and skills directly and, in turn, talking greater control over the projects they are responsible for. There is also the wider industry skills shortage to consider and main contractors are in an excellent position to nurture, support and celebrate this sector by making sure that the apprentices of today are in a position to create the national wealth of tomorrow.
Given the importance of construction to the wider UK economy, it is astonishing that the development of the next generation of skilled professionals is being handled so badly. According to government figures construction generates almost £117bn annually and employs over 2.4 million people. Furthermore, according to a recent report by the Confederation of British Industry (CBI), if the if the productivity of the industry rose by just two per cent, it could add £30bn to the UK economy annually by the end of this decade.
Tipping the balance
The role of subcontractors should not be undervalued or underestimated, as the majority are highly skilled and bring genuine value to a project. That said, the current overreliance on them is putting main contractors in an increasingly vulnerable position – something that is to the detriment of making sure that projects are completed on time, on budget and to the highest standards. Put simply, main contractors need to take greater responsibility for the overall supply chain, while also helping to ensure the longevity of the construction sector.
Tony Palombo is Managing Director for construction logistics at Wilson James. For over 25 years, Wilson James has been a leading design, planning and delivery provider of bespoke logistics solutions, which includes everything from site set up and organisation of accommodation for ground staff, to the management of secure materials movement around the construction site.
For more information, please contact www.wilsonjames.co.uk