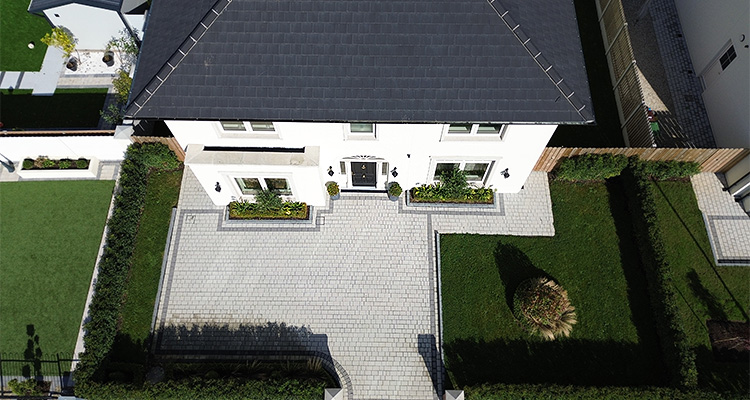
How O’Reilly Group’s modular solutions could ease the housing shortage while enhancing sustainability
Pioneers in precast construction, wastewater management, and paving excellence, the O’Reilly Group is a collection of three businesses – O’Reilly Precast, O’Reilly Oakstown, and O’Reilly Barleystone – offering Precast concrete, Architectural Paving and Environmental solutions around the UK and Ireland. With more than 85 years of industry-leading expertise, the Group combines traditional craftsmanship with the latest technologies to drive quality and identify sustainable solutions.
With ten production facilities across the UK and Ireland, The O’Reilly Group is well equipped to serve these geographies. The group’s priorities of quality, efficiency, and sustainability have earned a strong reputation and enabled the business to expand and diversify its comprehensive range of services.
As a leading manufacturer of precast concrete Buildings and precast architectural facades, O’Reilly Precast has an extensive portfolio and boasts an unrivalled track record in its design and build projects. The company’s products include full structural precast frame solutions, precast walls, full architectural precast frame solutions, prestressed walls, and precast columns and beams.
Driving growth
O’Reilly Oakstown, on the other hand, is dedicated to delivering state-of-the-art sewage and wastewater treatment products for both commercial and residential markets. With a range of sustainable solutions, the business meets clients’ diverse needs while ensuring compliance with ever-evolving regulations. On the domestic residential side, O’Reilly Oakstown offers efficient, reliable wastewater treatment solutions for individual homes, such as BAF 6 PE and BAF 8 PE wastewater treatment systems, precast concrete septic tanks, and rainwater harvesting systems. Designed to meet the rigorous demands of commercial and industrial applications, its commercial services include wastewater treatment systems, retaining wall solutions, and bespoke systems.
Lastly, O’Reilly Barleystone provides architectural paving brick, masonry brick, flagstones, and decorative stones, as well as expert advice to builders’ merchants, architects, designers, contractors, and self-builders. O’Reilly Barleystone’s product portfolio includes cobbled and smooth paving bricks, multi-sized cobbled and smooth paving, granite flags, textured flags, masonry blocks, and kerbs, setts, and circles.
Emmet Cosgrove, CEO of the O’Reilly Group, elaborates on the company’s evolution: “The Group started in 1939 and is now a third-generation family-run business. It started as a traditional sand and gravel quarry business delivering products to local customers, expanding in the 1960s and 1970s adding ready-mix concrete, blocks to its portfolio. We then progressed into agricultural precast solutions and then later into full frame precast building solutions.
“We’ve grown into one of the largest manufacturers of precast buildings for the residential, hospitality, commercial, and education markets in Ireland, and the UK. O’Reilly Precast is by far the largest division of the group, but Barleystone and Oakstown are rapidly growing, especially as we strive to offer more environmentally friendly products.
“Thinking about the architectural division specifically, we opened our O’Reilly Barleystone Division in 2011, growing it from nothing into a sizeable part of the group today. We have big plans to expand this division by a further 50 per cent in the coming years to meet ever-increasing demand,” he continues.
“With regards to our Precast Division, we design, manufacture and install highly complex Precast MMC solutions for our clients where the building is broken down into individual components that encompass insulation, windows, vents, and electrical sockets in place with and a brick finish on the outside and paint ready wall finish on the inside. By including these complexities, we can provide effective, rapid build, sustainable, structurally sound, and economically viable Precast solutions for our clients in both Ireland and the UK. We are finding that more and more developers & main contractors are adopting Precast MMC as a viable and sustainable solution to the residential property crisis in both the UK and Ireland.
“Despite our Architectural Precast Division being a relatively new addition to the Group, we’ve already completed several large residential projects in Dublin, including Deansgrange Residential Development, a development of 120 apartments featuring 5720 square metres of architectural wall panels, Belgard Square Apartment Block in Tallaght for JJ Rhatigan, a development of 200 apartments and Griffeen Point in Dublin for our clients Townmore Construction, a development of over 400 apartments. We’ve also completed several high-profile commercial projects in the UK, including the Terminal 2 Hilton Hotel at Heathrow Airport and the Hilton Hotel at Doncaster Racecourse.
“Introducing the architectural precast division has had a dramatic impact on the overall group and we’re set to increase production by 50 per cent in the first quarter of 2025,” Emmet explains. “We’re simultaneously expanding our production and ready-mix facilities to cope with increased demand, with both set for completion by April 2025. We’re confident that O’Reilly Precast will continue to flourish and drive major growth across the entire group in the years ahead.”
Specialist of choice
Turning to sustainability, Emmet shares how O’Reilly Group is embracing environmentally conscious practices. “Our vision for the future is to not only be the precast specialist of choice, but also the green specialist of choice,” he states. “We want to stand out from competitors when it comes to sustainability, and we’re constantly working to increase the amount of recycled content we use in our products, thus driving down our carbon footprint. We currently incorporate around 30 per cent of low-carbon cementitious materials into our precast solutions to lower the amount of cement required, again driving down our carbon footprint.
“We also use 100-per cent recyclable steel in our projects and have introduced several initiatives designed to reuse products or reduce waste. We’re recovering and recycling 80 per cent of the water we consume and reusing/recycling waste concrete where possible as part of our mission to achieve zero-waste-to-landfill status in the next two years. We’ve also introduced PV solar panels to reduce our energy dependence.
“As a group, we’re evaluating our emissions across Scopes 1, 2, and 3, and working closely with our cement partners to drive further change,” Emmet adds. “Our goal is to be net zero by 2050, and we are on track to reach our target of reducing our carbon emissions by 30 per cent by 2030.”
Family ethos
With continuous improvement in mind, investment is a key area of O’Reilly Group’s strategy. “We’ve invested heavily in technology to shape the way in which we design buildings, whether it’s design packages or systems that allow our different platforms to better communicate,” Emmet explains. “We’re always looking for innovative ways to streamline our operations. Our facilities vary in the level of automation; we have one facility operating with just three operatives, whereas another facility requires 30 people to generate the same level. Further automation will be introduced over the coming years as finding skilled operatives is becoming ever-more challenging. The next generation aren’t as interested in the construction industry as previous generations, and don’t see it as a viable career, in my opinion, which is disappointing and something we all need to address. It is one of the reasons why we’re seeing increased popularity and demand for our Precast MMC solutions.
“However, we’re fortunate to have an amazing team of energetic individuals that facilitate our fantastic work culture,” he reflects. “Our retention levels are high, and we have some employees who’ve been with us for more than 40 years. Although we’ve grown to be a large company, we’ve retained the family ethos that always existed here”.
As our conversation closes, talk turns to O’Reilly Group’s future, which is sure to be bright with Emmet at the helm. “Our investment for 2025 is focused on further expansion of our architectural wall division, as well as our O’Reilly Barleystone division and our ready-mix concrete division,” Emmet concludes. “Although we’ve expanded substantially over the last five years, we have an ambitious business plan to expand further over the next five years through organic growth and strategic acquisitions that will complement our product portfolio.”