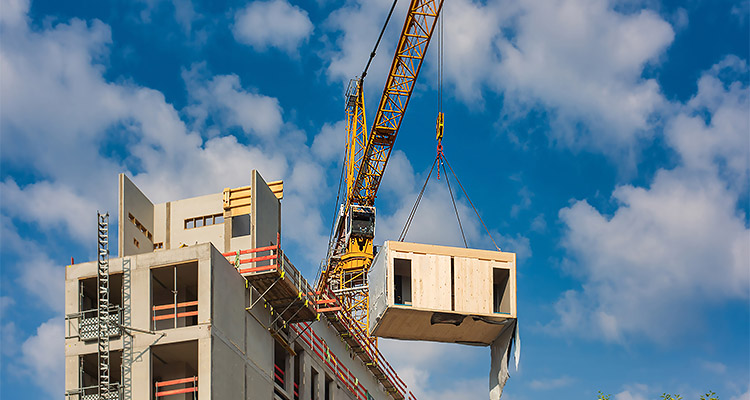
Is the future of construction pre-built?
Modular construction has quickly evolved into one of the most efficient construction techniques in the industry, offering a variety of benefits that traditional on-site construction methods can’t compete with. The flexibility of the designs means the shapes and sizes of buildings can easily be added to, modified or restructured to accommodate changing requirements or expansion projects.
As stricter regulations are continually introduced to improve energy efficiency standards, is there an unidentified, but detrimental, issue with modular buildings? Could these steel frameworks that fit together like jigsaw pieces make any efficiency achievements redundant due to the impact of thermal bridging? Paul Beech, Director of thermal break specialists, Armatherm, discusses the future of modular construction and how to ensure structures created with this technique continue to pave the way for efficient building.
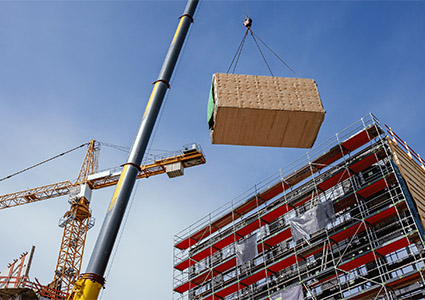
Getty.
Modular construction is often praised for its precision and sustainability. Built in controlled environments, modules are carefully insulated, airtight, and designed to meet stringent energy efficiency standards. However, while these individual sections may perform exceptionally well in isolation, the way they connect on-site can create serious inefficiencies through thermal bridging and the impressive accreditations they’ve earned as individual elements can prove ineffective once in situ.
Thermal bridging occurs when highly conductive materials, like steel which is often a go-to in modular projects, form a pathway for heat to escape through a building’s structure. In modular buildings, this is particularly problematic at the points where the modules are joined to create a full structure. The steel framework acts as a bridge, creating a pathway for heat transfer, bypassing the insulation and undermining the energy efficiency of the entire building.
So, although it can be easy to assume that factory-built structures can perform just as well on-site, we can see that this is not always the case. The connections where steel framework joins can present opportunities for thermal bridging, causing a whole host of detrimental issues.
Thermal bridging is a flaw that can lead to increased energy consumption, higher bills, and even long-term structural issues within a build. When energy is given the opportunity to transfer at these joints, it forces heating and cooling systems to work even harder to create and maintain required temperatures, increasing energy usage. For example, cold storage units need to be kept at low temperatures, if these are in warmer climates there’s opportunity for heat to enter via thermal bridging and vice versa with buildings that need to be kept warm in cooler environments.
When conflicting temperatures meet, the resulting humidity can create condensation on interior surfaces. Left unchecked, this excess moisture can lead to significant structural issues, including dampness and the gradual degradation of building materials. Over time, this weakens the integrity of the structure, leading to costly repairs and potentially shortening the building’s lifespan. Beyond structural concerns, condensation also creates the ideal environment for mould growth, which poses serious health risks to occupants, particularly those with respiratory conditions. Additionally, the increased need for heating and cooling systems to counteract heat loss or gain through thermal bridges leads to skyrocketing energy bills, reducing the overall cost-effectiveness of modular buildings. Not only do these challenges create immediate concerns for individual projects, but they also raise broader questions about the long-term sustainability and resilience of modern construction. If left unaddressed, thermal bridging could undermine the very benefits that make modular construction so appealing – efficiency, speed, and sustainability.
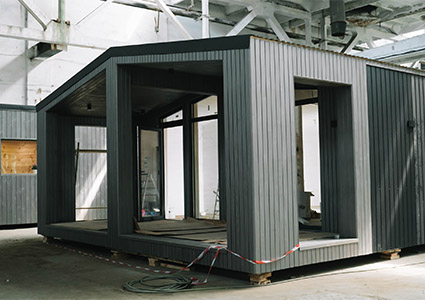
As modular construction continues its rapid expansion, so too does the need for innovative materials and smarter construction techniques to ensure long-term performance. The industry is seeing a shift towards solutions that not only improve energy efficiency but also futureproof buildings against changing climate conditions and evolving regulatory standards. With sustainability becoming a top priority for developers, architects, and policymakers alike, addressing thermal bridging will be critical to maintaining the reputation of modular buildings as a forward-thinking, eco-friendly alternative to traditional construction.
In any construction, integrating effective thermal breaks is vital for enhancing energy efficiency. These materials, designed with low thermal conductivity, act as barriers to disrupt continuous heat flow, significantly reducing thermal transfer. Solutions like those from Armatherm can be seamlessly incorporated into the steel framework of modular buildings to minimise thermal bridging. The FRR structural thermal break material combines excellent thermal insulation with high compressive strength and has been successfully implemented in numerous structural steel connections, effectively transferring load in both moment and shear conditions.
Ultimately, while modular construction delivers notable advantages in efficiency, speed, and sustainability, addressing thermal bridging is key to optimising these benefits. Thermal breaks play an essential role in preserving energy performance, reducing heat loss, and preventing issues like condensation and material degradation. By prioritising advanced thermal break solutions alongside precision in design and installation, modular construction can continue to set new standards for high-performance, energy-efficient buildings.
Armatherm™ is one of the leading suppliers of structural thermal break materials for the construction industry. Armatherm™ thermal bridging solutions can be used anywhere a penetration or transition exists in a building envelope creating a thermal bridge. Armatherm™ structural thermal break materials minimise heat loss at balcony, canopy, parapet, masonry shelf angle, cast in situ and cladding connections.