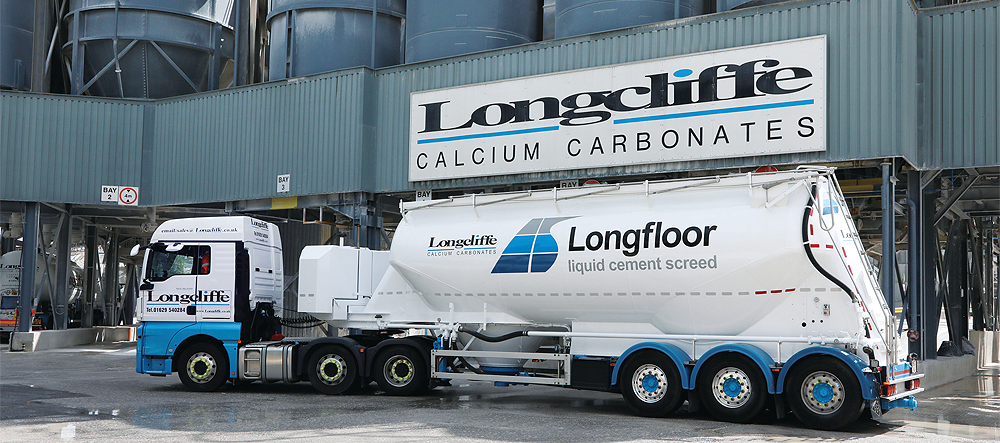
Longfloor
Cementing a legacy
Flowing screeds have been used in the construction industry for more than 20 years. During this time, what can be referred to as the ‘Holy Grail’ for manufacturers, has been the creation of a cement-based liquid screed, whose properties countervail some of the inherent disadvantages of both traditional screed and the calcium sulphate-based liquid screed, also known as anhydrite screed. Owing to the technological developments in the additives that are put in a screed over the last three years, this goal has now been attained.
One of the leading products of cement-based liquid screed is Longfloor. Produced by Longcliffe – the UK’s second largest industrial grade limestone powder manufacturer and supplier – Longfloor is a dry powder bulk binder that consists principally of very fine, high-purity ground limestone and a suite of dry chemical reagents and admixtures that control shrinkage and stability, and add plasticity to the mix.
“Liquid screeds, in general, hold multiple benefits over traditional ones,” begins Longfloor’s General Manager, Darren Williams. “They are easy to install and can be laid more thinly on a floor than traditional screeds, which makes them an ideal solution for underfloor heating, as you get a better thermal conductivity.
“Then, if you were to compare cement-based and anhydrite screeds, the former gives you all the benefits of the latter with the additional advantage of its drying out three times quicker than an equivalent anhydrite screed,” Darren continues. “Furthermore, you do not have to do anything to the surface before you bond your floor finishes, so you can lay the finish directly onto the screed. Longfloor can be used on acoustic installations, floating floors or directly over underfloor heating pipes. It can also be un-bonded over a separation membrane.”
Complete control
Moving on to discuss the process of producing and supplying Longfloor, he points out that Longcliffe manufactures the binder from a state-of-the-art milling and blending facility in Derbyshire, whose setup cost the company just under £1m. “It is one of our biggest strengths that we have complete control over the manufacturing process, because we have everything we need here in Derbyshire, with the main raw material coming from our quarry in the Derbyshire Dales. As we employ our own equipment and staff at every stage, we can also provide traceability and guarantee the consistency of the product’s quality.
“When the binder is manufactured, it is then sent to a ready-mix concrete plant, where they add cement, sand, and water to the product to create the liquid material, which is subsequently delivered to sites either in a volumetric mixer or a traditional concrete truck mixer,” Darren explains. “It bears mentioning that we not only supply the main constituent part of the screed, but we also pre-verify all of our customers’ formulations. We take their sand and their cement to test them in our facilities for aspects such as mix fluidity, compressive strength, flexural strength, and shrinkage. We do all of that in-house and only when we have been assured of the suitability of our customers’ raw materials, do we allow them to produce our product.”
Talented professionals
The expertise demonstrated by Longfloor’s workforce from technical, as well as from sales perspective, is highly valued by Darren. As he remarks, “our team is part of our offer to customers.” The business has carefully grown a team that involves some of the most talented professionals across the industry to take care of the specific needs each client may have.
The very same people have also been behind the development of Longfloor’s latest product that will be officially launched at the UK Concrete Show on 25 and 26 March 2020. Darren details: “One of the processes that have historically been inseparable from a cement-based liquid screed, is the spraying of the screed with a curing agent to prevent the surface from drying out too quickly. This has always created a bit of an issue, because you are practically at the mercy of the person who is spraying the material on, as it has to be ensured that they have the right equipment and the right curing agent, and that they will adhere to the right dosage.
“What we have done, is a develop version of Longfloor called IntegraCure that has a curing agent fully integrated within the screed. It represents a landmark shift in technology, which will dispense with the spraying operation and will result in a significant change in how screeds are laid.”
It will be Longfloor’s second appearance at the Concrete Show and Darren offers his opinion on why it is beneficial for the company to be at the event: “Ours is still a young product and as such, it is essential to get our name in the marketplace and show the world that we are here and available. The Concrete Show provides a good medium to do that, it being Europe’s leading specialist concrete event.”
Straight after the production of Longfloor began, Longcliffe set out to grow a network of stockists across the UK, in order for the product to obtain a full national coverage. According to Darren, the organisation is halfway through the completion of the goal. “We still have work to do before we are satisfied with the base of suppliers we have in place, but once this is done, we have big ambitions for the product.”
He concludes: “We want to develop the brand further and raise product awareness in the next five-year period. We plan on focusing more on the solutions Longfloor brings for each of its applications, so there are numerous growth opportunities for us in the coming years that should allow us to expand our presence in the market.”
Longfloor
www.longfloor.co.uk
Products: Dry powder bulk binder for the manufacture of a cement-based liquid screed