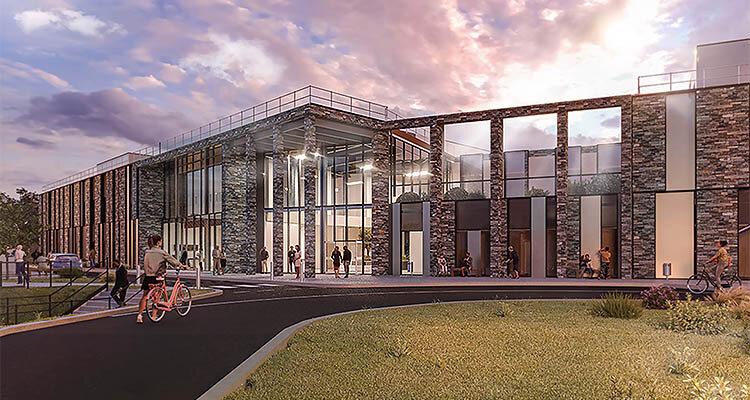
Merit employs advanced technologies and sustainable solutions to design and build better buildings
As a leader in the UK’s construction industry, Merit is renowned for its technically complex, high-quality buildings. Through industrialised construction and digital manufacturing, the company completes a range of projects for the healthcare, biotech and pharmaceutical sectors in just one third of the time compared to traditional methods of construction. Its use of advanced 4D Building Information Modelling (BIM) technology and a product-based approach are a testament to its modernity, enabling the delivery of exquisitely unique buildings. Recognising its clients’ need for swiftly delivered, highly functional, and affordable facilities, Merit has adopted an industrialised construction business model using a unique proprietary product platform.
Innovative solutions
Merit’s product-based approach exceeds government initiatives such as Construction 2025, by prioritising a zero-carbon emissions design philosophy throughout its offsite manufacturing process. This commitment allows the company to actively work towards a more sustainable environment in the here and now, instead of treating it as a future concern. Merit’s diverse portfolio of products caters to a wide range of settings such as vaccine facilities, theatres, hospitals, pharmacies, laboratories and many more. One of its standout offerings is UltraPOD® – an expandable, versatile, and full building solution. UltraPOD® can be used as a standalone building or can be combined with multiple UltraPODs® to create a larger building. Each UltraPOD® is made up of several offsite manufactured components and products, which can be mixed and matched based on customer priorities. Indeed, the product offers countless customisation options including building scale, height of cleanrooms and manufacturing equipment, project timescales, site constraints, and budget considerations. This adaptability ensures that Merit can satisfy client requirements and preferences, which, in turn, has a positive impact on reputation and customer retention and acquisition.
Another product is the FLEXI POD®; a hybrid solution of traditional build, comprising aspects of MMC for the shell and core, and an offsite manufactured fit-out which is facilitated through a Pre-Assembled Module (PAM) and POD strategy. FLEXI POD® is designed based on a successful GMP compliant and regulatory approved MEP/architectural design platform which is adapted to customer specific applications and is deeply integrated into the validation process in order that a more productive, consistent and successful outcome is achieved.
Spanning a staggering 263,000 square feet, Merit’s offsite manufacturing facility is one of Europe’s largest of its kind. Today, Merit pioneers a new industrialised approach that places technology adoption and innovation at its core. Offsite manufacturing accounts for 75-to-95 per cent of Merit’s work, allowing the company to deliver projects faster, at a lower cost and with sustainability in mind. Thanks to recent developments in BIM and REVIT technologies, Merit has drastically moved away from traditional onsite construction methods towards factory-manufactured subassemblies and complete POD solutions. 2019 was a significant year for the company as it marked the completion of Merit’s very first entirely offsite manufactured project for Cell and Gene Therapy Catapult (CGTC).
Productive partnerships
A centre of excellence for innovation, CGTC’s core purpose is to build a world-leading cell and gene therapy sector in the UK. For several years, Merit has been undertaking extensive design and construction works at CGTC’s £70 million advanced manufacturing facility in Stevenage. This includes the construction of a new office to accommodate additional space requirements. Additionally, Merit oversaw the design and subsequent delivery of six cleanroom Good Manufacturing Practice (GMP) production modules, ensuring adherence to strict quality control guidelines and regulations for the production of pharmaceutical and healthcare products. Keith Thompson, CEO of CGTC, sang high praises of the project. “We are very pleased to be able to double the existing capacity of the CGT Catapult manufacturing centre with help from our partners Innovate UK, UKRI and the industrial challenge fund as well as the European Regional Development Fund. Working with Merit on this expansion phase and using an innovative method of construction with their offsite prefabricated building techniques has been a real advantage in ensuring we could maintain complete functionality of our fully operational facility ensuring minimal disruption to our collaborators. Thanks to this approach to building GMP facilities, the expansion phase has come online very quickly and will leverage the existing operational systems for more companies to set up rapidly.”
More recently, Merit secured the main contractor role for the UK’s inaugural CAR-T cell manufacturing facility in 2021. Autolus Therapeutics, a biopharmaceutical company specialising in next-gen T cell therapies, is expanding its capabilities with a new 7500-square-metre facility in Stevenage. The facility aims to develop CAR T-cell therapies for cancer treatment, with the capacity to process 2000 treatments annually.
Sustainable design
The collaboration involves Merit, Autolus, and developer Reef Group, with funding support from UBS Asset Management. Through intelligent use of a vertically integrated platform design and Virtual Design and Construction (VDC) technology, Merit concluded the first construction phase including Grade C Cleanrooms for Autolus Therapeutics in 17 months; with only 12 months spent on site. This included concept design, planning, commissioning, and validation. Traditional construction projects also take months to commission and validate, whereas Merit’s approach for Autolus took only eight days.
Merit’s commitment to driving measurable improvement for sustainability means that the facility has been designed to BREEAM Excellent rating. Merit also has a 6D BIM rollout strategy in place. Working closely with its Net Zero consultant, the team has produced a case study for the Autolus Therapeutics facility. With meticulous detail, Merit can assign Scope 3 carbon values on a component level within the digital twin to understand where Scope 3 carbon emissions are concentrated. It’s clear that the business is making a concerted effort to reduce these as quickly as possible to adhere to its 2030 targets.
Last, but certainly not least, towards the end of 2023, Merit secured a contract from University Hospitals Birmingham NHS Trust Foundation. The £25 million project involves designing and delivering a state-of-the-art Elective Hub (Operating Theatre Block) at Solihull Hospital.
The project, a ‘first-of-its-kind’ for Merit, encompasses a two-storey building housing six high-quality theatres, including three ultraclean and three robotic ones, along with supporting services. The development aims to significantly enhance the hospital’s capacity for elective procedures, with an estimated additional 15,000 treatments annually. The project is expected to be completed by May 2024.
Turning towards sustainability, while climate change continues to exert pressure on businesses around the globe, Merit has implemented a zero-carbon emissions design philosophy at the heart of its offering. Through intelligent use of new technologies, renewables, heat pumps and heat recovery systems, it demonstrates the feasibility and economic viability of producing buildings that are zero Scope 1 carbon in operation enabled.
Aligned with the company’s offsite manufacturing approach, this strategy not only eliminates the reliance on fossil fuels within buildings but also significantly minimises the carbon footprint associated with travel and material logistics resulting from undertaking construction in a manufacturing centre rather than on site. Furthermore, Merit’s entire range of offsite manufactured products have been assessed by an independent Building Research Establishment Environmental Assessment Methodology (BREEAM) advisor and achieve BREEAM Excellent as a minimum.
Through its innovative offsite solutions and zero carbon emissions design philosophy, Merit is poised to positively transform the future of construction.