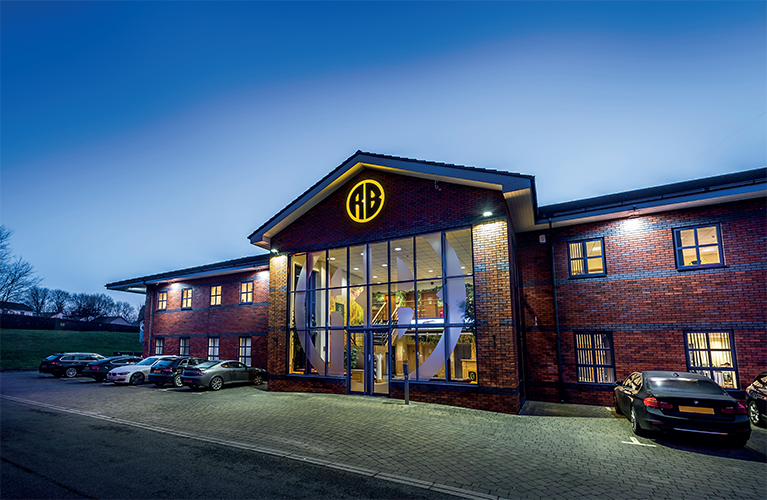
Roger Bullivant Ltd
Building solid foundations
As one of the UK’s leading foundation engineers, Roger Bullivant Ltd continues to be known for its dedication to safe, sustainable practice
Specialist foundation engineering company, Roger Bullivant Ltd (RBL), sees ongoing success, as it continues to produce durable, expertly designed foundations to a wide range of customers across the UK. With a team of highly trained professionals, and a series of major accreditations under its belt, the company now looks to make further investments in organic growth and has a commitment to continue to deliver modern methods of construction.
Working effectively within its niche, RBL provides an unparalleled depth of knowledge to clients in the construction industry; as Cliff Wren, Managing Director at RBL, details: “Roger Bullivant Limited is a Foundation Engineering Company specialising in the design and construction of foundations for all types of buildings and structures, in all kinds of ground conditions. Our foundation designs are individually engineered to satisfy project and customer needs, with a focus on value engineering.”
The company operates across the UK, using a comprehensive network of offices and a centralised, in-house manufacturing facility. “We operate from our head office in Swadlincote in South Derbyshire, and we have eight regional offices, including an office in Wales and one in Scotland. Our manufacturing facility is located on the same site in Swadlincote, and can produce over one million metres of precast concrete piles every year, together with 180,000 linear metres of precast beam.
“We are part of the global Soletanche Freyssinet Group, and report directly into one of its main subsidiary group organisations, Soletanche Bachy, all of which is part of the VINCI Construction group,” Cliff explains.
The company’s focus on sustainability and safe, secure practice has helped it achieve major accreditations over the last 12 months, including being named ‘Business of the Year 2021’ at the East Staffordshire and South Derbyshire Business Awards. As Cliff enthuses: “Our success at the Business Awards was one of real pride to the business.
“It was the first time we had entered the awards, and we were shortlisted in four categories. To be named ‘Business of the Year’ was a real honour. Our team is very proud of the achievement, as this success was down to their hard work across all areas of the business.”
One of RBL’s unique selling points is its range of precast products, which are designed and built in the company’s own manufacturing facility. “Our large factory in Swadlincote manufactures all our precast items, and distributes them nationwide. The factory was commissioned in 2017, and was designed to introduce the latest automation technology to our operation.
“All our concrete is batched on-site, using locally supplied materials, which allows us to closely manage quality and environmental impact. We engage with industry specialists to stay informed of the latest technological advances, and our most recent initiative is a review of material flow and robotic welding technology,” confirms Cliff.
RBL’s products are designed to be both effective and malleable, in order to meet the requirements of as many applications as possible. They are also made to optimise the safety and sustainability of RBL’s operations, as Cliff discusses: “Sustainability based projects feature highly within our current portfolio, and quite rightly so. For example, our Continuous Displacement Auger (CDA) is a tool we have developed and deployed to compete against traditional Continuous Flight Augers (CFA).
“The key difference here is that CDA displaces and improves the ground, whilst CFA removes and replaces it. This means that piles can be shorter for a given load, generate very little spoil, use less material, and increase productivity. These benefits all help reduce our embodied carbon, leading to reduced fuel because of the shorter programme and fewer truck movements, removing spoil or delivering concrete.
“We are also improving our concrete mix design at the moment, by reducing the embodied carbon in our concrete. We are achieving this by replacing 50 percent of our cement-holding materials with Ground Granulated Blast Furnace Slag (GGBS); we plan to increase that percentage further in the coming months.”
The company’s dedication to research and innovation has helped it produce some of the industry’s most cutting-edge foundational engineering products. “At Roger Bullivant Limited we have a diverse approach to research, development and innovation, covering every aspect of the business. This relies on building an innovation culture, wherein all of our staff are encouraged to challenge current practices, and to suggest improvements. These suggestions are then evaluated and prioritised based on their opportunity and feasibility against our core strategic pillars of safety, profit, work winning, people and innovation,” reveals Cliff.
In the last two or three years, this approach has led to the release of numerous new techniques, processes, and improvements. “The key to our success is clear project definition and aims, followed by rigorous testing, evaluation and detailed documentation. All these things rely on our greatest asset: our staff.
“Sharing these improvements is also important; whenever a new project is released, it is shared on our intranet, and in our company magazine. We also provide internal and external webinars to promote the uptake of new products and processes. These are a great way to share what works, as well as opportunities for improvement.
“In addition, we recently held a series of three webinars covering housing foundations in the residential market, showcasing one of our projects in Surrey. This series covered everything, including identifying the requirements for the job, the design element, manufacturing the product, pile installation, beam installation and client feedback. This series is important as it shows clients and prospects what we do and how we work, so they can be more informed on our processes and techniques,” Cliff asserts.
Roger Bullivant Ltd was recently appointed to provide residential foundations on the £115 million Partington Housing Scheme at Heath Farm Lane. The joint venture, formed by Vistry Partnerships and the Trafford Housing Trust, is one of the largest regeneration schemes in the Greater Manchester area, delivering 600 new homes. “RBL was required to provide a cost-effective piled foundation solution in a safe and timely manner, dealing with the issues associated with the regeneration of a brown-field site, and the associated variable ground conditions, access, and environmental considerations.
“Following early consultation with Vistry, we decided that the best way forward would be an offsite solution for the piles and ground beams. This high-quality engineered foundation system is factory produced, removing all quality and waste issues from site. This is in line with Vistry’s commitments to reduce waste and packaging. It was agreed delivery would be phased, in order to achieve the best commercial results,” Cliff reports.
This project highlights RBL’s range of capabilities, and speaks to its values as a people and community driven operation. As a business, RBL is characterised by its dedication to steady growth and sustainable practice. It comes as no surprise that this mission is central to the company’s plans for the future, as Cliff concludes: “We are looking to grow as a business in 2022, not only in terms of turnover, but also looking to invest in new plant and equipment. Over the next three-to-five years we have a commitment to look into more sustainable initiatives, and build on the ones we have in place.
Roger Bullivant Ltd
https://www.roger-bullivant.co.uk
Services: All-terrain foundation engineering