Where innovation meets sustainability: Blue Phoenix produces a proven alternative to primary aggregates that is circled back into the economy
As one of the world’s leading processors of Incinerator Bottom Ash (IBA), Blue Phoenix is responsible for diverting millions of tons of waste material each year from landfills. Working closely together with partners in the Energy-from-Waste (EfW) sector, the company has made great strides towards its mission of building a sustainable future. Blue Phoenix takes the residue ash from an EfW facility, separates the ferrous and non-ferrous metals, and produces an IBA Aggregate (IBAA) that is circled back into the economy and used as a sustainable alternative to primary aggregates. Having seen success throughout the UK, Europe and the US, Blue Phoenix is now looking to expand its horizons even further, as Chief Executive Officer, Paul Knight, explains: “There are strong markets for IBA operations across Europe, and we’re now working toward expanding globally into new and developing markets. We’ve most recently built Australia’s first IBA processing facility, in 2022, working hand-in-hand with Australian authorities on the regulation around the safe and responsible use of IBAA in the Australian market.
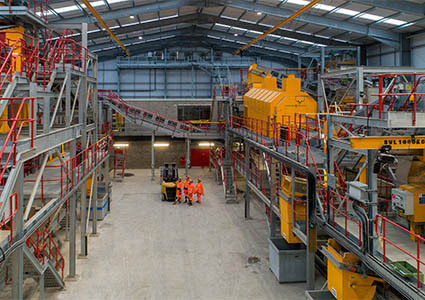
December 2 2019
Matthew Power Photography
www.matthewpowerphotography.co.uk
07969 088655
matthew@matthewpowerphotography.co.uk
@mpowerphoto
Research and innovation
“Following this venture in a completely new market, our team is currently working with Dubai Municipality, with the ambition of closing the loop on the UAE’s first EfW facility. With over 20 years of experience, we leverage our global scale and advanced operational capabilities to bring custom solutions to meet the needs of country-specific environmental legislation. We strive to develop new pathways that will allow us to expand our range of services. One of our upcoming goals is to implement APCr services, which is essentially a method of pollution control. Our Research and Innovation (R&I) team are continuously looking at new ways to implement IBA, so that it can be used on a smaller scale in countries where the legislation is more stringent.
“For example, we have developed an innovative wet processing solution to assure the right quality output in line with regulation for the Green Deal in The Netherlands. We use in-house developed and patented technologies in combination with industry-standard equipment to design and build efficient processing installations. The clean aggregates produced are suitable for civil work and can be used without restrictions in The Netherlands. For other regions, we adopt a similar approach with our dry processing technologies.”
Cost-effective material
Blue Phoenix operates 26 facilities globally, with an excess of 3.5 million tons of waste material every year being turned into secondary aggregates than can be used in a variety of applications. Paul explains: “Sustainability is at the heart of our business; with significant investment committed to reducing the carbon emissions of our own operations, as well as engaging with stakeholders to better communicate the benefits of using recycled metals and secondary aggregates.” IBAA is an extremely cost-effective material when compared to primary aggregates and Blue Phoenix is working towards a verified Carbon Footprint. There are also advantages logistically when using IBAA due to the low density of the material allowing for fewer vehicle movements as this gives volumetric advantages over primary materials.
Working on a global scale, and processing millions of tons of materials coming from various sources of varying quality, Blue Phoenix’s operations requires constant innovation to maintain a reliable output. Paul shares some insight into Blue Phoenix’s approach to innovation: “At the group level, we have a research and development team. They are focused on looking for new technologies and applications. The tools we have available are always developing, which presents opportunities for expanding our business into new areas. We’re currently looking at cementitious materials for application in the cement industry, which has the potential to make a huge impact on reducing carbon emissions in what is known as being a very carbon-intensive industry. There’s also emerging technology that can remove single source metals under the right conditions. That works for some areas, but not others, yet. It’s all about balancing the research and development with practical applications across our different sites and regions,” he asserts.
Making a difference
With new sites opening across the world, and exciting new technological developments being made each day, there’s no doubt that Blue Phoenix’s journey has only just begun. As Paul concludes: “This group has a long-standing future ahead of it, supported by multiple investments into other divisions that all complement one another. At the moment our business is made up of over 600 employees, and I would like to see that double in the next five years. It’s also really important that the company moves into new market areas, pioneered by new technology. One thing we are very clear about is that we want to offer more than one solution. Reaching zero-waste to landfill will require more than a one-size-fits-all approach, and we’re focused on moving this market forwards, effectively, so that we can make a real difference.”