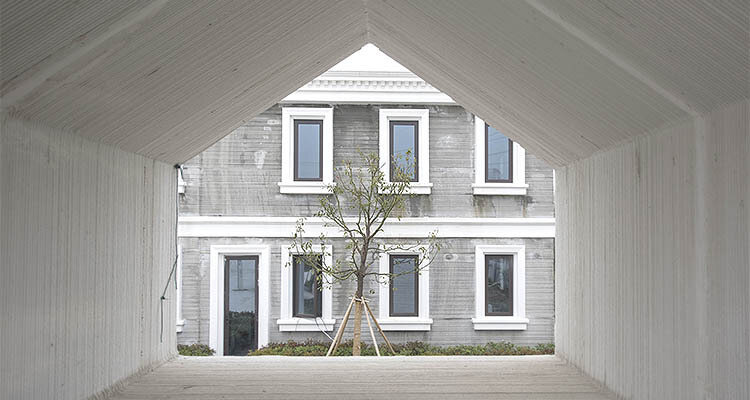
Zenab Khatun asks: are 3D printed homes finally gaining market traction?
As the construction industry grapples with the challenges of meeting the government’s affordable housing targets and striving towards net-zero goals, 3D printed homes have gained momentum as a possible innovative solution. What are the advantages of this transformative technology over traditional construction methods, and what do contractors and developers need to be aware of?
Utilising concrete as their primary construction material, 3D printed homes are typically assembled by robotic arms that build layer by layer in a process called ‘contour crafting’, enabling the creation of highly customised designs.
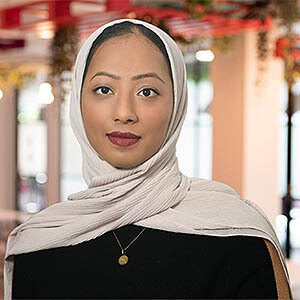
This unique approach allows for the creation of curved shapes and hollow spaces within the walls designed for insulation, enabling high standards of energy efficiency. Additionally, the construction process generates significantly less waste than conventional building methods, further bolstering its eco-friendly credentials, and the materials required to build, such as concrete, are often more cost effective.
One of the key advantages of 3D printed homes is the increased efficiency during the construction process. While human oversight, engineering and monitoring remain essential, the reduced need for on-site workers dramatically decreases the risk of injury.
Nevertheless, it is crucial for developers and manufacturers to acknowledge the legal risks associated with the interaction between workers and heavy machinery. Taking steps to ensure all health and safety protocols are in place and understood by the operation and construction teams is imperative.
Challenges and market resistance
While the 3D printing process offers benefits in terms of build time and material efficiency, its potential to reduce the demand for construction labour is a point of concern, which could be a contributing factor to the slow adoption of this technology.
Another potential area of resistance is that 3D printed homes, along with other modern methods of construction (MMC), can be seen as disruptors to the traditional mass housing development approach.
The benefits of 3D printed homes are mostly geared towards the buyers, rather than developers, and with little cross-sector collaboration as to how to make the most of these new technologies, it can be difficult for developers to see the advantages that 3D printing can bring.
For example, most current housing developments built by 3D printers are intended for the homeless or for those less able to afford traditional brick-and-mortar homes. There is a huge area of opportunity here for 3D printed housing developers to work in conjunction with the rest of the housing market to provide the affordable homes that all too often fall by the wayside.
There is also the risk of an increase in intellectual property claims against developers. For example, intellectual property right holders may seek to enforce their rights if they are infringed by any form of the 3D printing process.
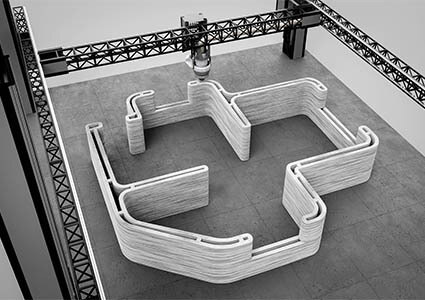
Navigating legal and contractual considerations
For 3D printing to become a more popular method of construction, it would be useful for the industry to have a bespoke contract for this method of construction, similar to NEC4, which also accommodates modular construction. This would assist developers to consider various contractual considerations, including the usual risks and obligations. For example, risk management in the instance that defects arise, ensuring the printing machinery is in good working order and materials are sourced correctly to meet the construction timeline and budget are essential.
Furthermore, accountability for the quality of materials and machinery used in the 3D printed build must be established to assure customers the home will meet agreed-upon standards and be safe, comfortable, and insurable. Therefore, a robust selection process for sub-contractors and operators, coupled with meticulous due diligence activities, is essential to identify and mitigate potential risks.
Given that 3D printing in construction is a relatively new technology, additional regulations may be introduced as it gains popularity to ensure on-site safety, especially when workers interact with heavy machinery.
Developers venturing into the 3D printed space must remain fully aware of emerging regulations and legislation, including broader industry standards such as the Building Safety Act. Seeking professional advice when necessary is prudent.
The path forward
As long as profit remains one of the main drivers for the housing sector, 3D printed homes could face the same frustrations that MMC has faced and a real battle for mass adoption. However, what is clear is that there is a great case to be put forward that envisions 3D printed homes working in tandem with traditional developments. They can be built faster, more efficiently and for a relatively lower cost, providing an interesting potential solution to the housing crisis in the UK.
These homes could become gamechangers for those on low incomes or those struggling to afford to buy in the current economic climate, and with developers, government officials and local authorities all looking for solutions, 3D printed homes may yet provide part of the answer.
www.shma.co.uk
Zenab Khatun is a construction trainee solicitor at law firm Shakespeare Martineau. Working with organisations of all sizes, the firm delivers a broad range of specialist legal services and has expertise across multiple areas including but not limited to energy, education, banking and finance, healthcare, investment funds, manufacturing, agriculture, family business, Islamic finance, later living, social housing, charities and real estate. Shakespeare Martineau also provides services for families and private clients.